Popularization and application of automatic seam welding machine for high speed steel drum
Shenzhen Juntengfa Automation Welding Equipment Co., Ltd. Zhu Haiying Wang Jinghua
Keywords: steel barrel seam welding energy saving high speed automation
0. Preface
China's steel drum products are mainly 200L closed steel drums, and the welding production of steel drums has always been based on general-purpose semi-automatic seam welding machines, as well as some enterprises to carry out combined transformation and semi-automatic seam welding machines. Primary automatic seam welder. However, compared with the advanced automatic seam welding machines in the international arena today, it is far from meeting the needs of domestic and international markets, and it is not able to meet the needs of the rapidly growing steel drum market. At present, the fact that China has joined the WTO and China's international processing industry has greatly increased the demand for steel drums in terms of quantity, type, quality and form. The current steel barrel production methods have not been able to meet the demand for this quantity and quality.
One. Introduction
Shenzhen Juntengfa Automatic Welding Equipment Co., Ltd. based on its own welding equipment production experience and automation development and research and development advantages, combined with the domestic steel barrel manufacturing production experience, the introduction and digestion of international advanced steel barrel automatic seam welding technology, absorption and improvement Develop, design and produce a new high-speed steel barrel automatic seam welder. The equipment is an important equipment for high-speed production of metal barrels. It is a composite automatic welding equipment that integrates feeding, feeding, reeling, welding, rolling weld, cutting tongue and unloading. The control adopts high anti-interference PLC programmable controller and modular circuit. The welding power source adopts DC welding power source with constant voltage/constant current function and programming control technology to ensure the welding current and the fluctuation of individual external factors in different parts of the workpiece. The impact on the quality of the weld.
The rated power of the equipment is 3-phase 150KVA, 380V three-phase input, secondary rectified DC output, saving about 30% of energy compared with other industrial frequency AC power, and will not cause disturbance to the grid when AC power is welded and three-phase power is not Balance impact. The welding speed is up to 16 meters per minute and the highest productivity is 720 pieces per hour. The welding range is up to the international standard steel drum with a diameter of 571.5mm. The length can be from 470mm to 1100mm. The thickness can directly match the international thin plate trend. The welding can be carried out from 0.5 to 1.5mm, so that the production can not only save material and cost. It can also meet the needs of the international market. The steel drum material can be carbon steel, alloy steel and non-ferrous metal.
The reel of the FNT-3×150 high-speed steel drum automatic seam welding machine is welded to the longitudinal weld seam in one piece of equipment, eliminating the need for spot welding of the weld seam and improving production efficiency. The welding speed, welding current, electrode pressure and other parameters are easy to adjust, and the amount of edge is stable and reliable. The weld is rolled through two passes to further improve the quality and the surface of the workpiece is smooth and beautiful. The electrode wheel can trim the electrode wheel without disassembling, which improves maintenance efficiency. The control system adopts man-machine interface, touch control, full Chinese operation, direct display of fault status, and convenient and quick maintenance.
The process flow is shown in the figure
The specific process is as follows:
Unloading: The material to be processed is introduced into the blanking device, cut according to the width of the required material, and then sent to the feeding device to wait for the advancement circle.
Reel: The automatic feeding device automatically pushes the cut steel drum sheet into the reel part integrated with the whole machine according to the working condition of the next process, and the cut steel plate is rolled into a barrel of corresponding diameter according to the need. shape.
Conveying: The barrel body is transported to the position to be welded by a variable frequency motor, a chain transmission device, etc., and then the barrel body is advanced to the inlet of the welding wheel by the propulsion unit according to the welding station position.
Positioning welding: The welding station consists of three sets of shaping wheels and upper and lower welding wheels. According to the adjusted special heat control program, the automatic adjustment of the slow rise, impedance change, slow drop and net pressure change is ensured to ensure the welding quality. The side width is only 3~4 mm. The welding wheel can be automatically displaced laterally, which greatly extends the service life of the welding wheel.
Rolling and shaping: During the working process, after the barrel leaves the welding wheel, it enters the rolling wheel that runs synchronously with the welding wheel. At this time, the weld of the barrel is still in a red hot state, under the pressure of a certain pressure, The internal structure becomes more compact, the steps of the weld lap are reduced, the overlapping thickness at the lap is reduced, and a flat, smooth and beautiful flat weld is formed.
Cut the tongue: Cut off the welded joint at the welded joint to facilitate the next process.
Shape and structure as shown
The device operating system is divided into three major operating modes: automatic loop operation; step operation; segmentation operation. Some of the operation interfaces are as shown below:
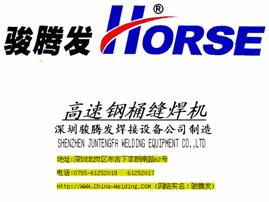
Boot interface
Production preset interface, scheduled production
The fault message display interface prompts the location of the fault to facilitate maintenance and maintenance.
Operation mode selection interface for selecting different operation modes
Welding parameter adjustment interface to adjust the welding current and the slow rise and fall of different areas
The maintenance setting interface prompts the set number of times of lubrication, refueling, cleaning electrodes, etc., to ensure the safe and reliable use of the equipment, and reflects the humanized side of the equipment.
two. Characteristics
1. High speed: high degree of automation, high productivity, continuous continuity, up to 720 workpieces per hour. Since this equipment is actually a combined high-speed seam welding equipment for coil and welding, the time required for each step can be overlapped (seven steps overlap), and one operator can also complete the operation of the entire equipment. And monitoring, compared to the current domestic steel barrel seam welder, it is called "high degree of automation, high productivity, strong continuity."
2. The welding range is wide: metal barrels with carbon steel and alloy steel with a length of 480 to 1100 mm, a maximum diameter of 571.5 mm and a thickness of 0.5 to 1.5 mm are used as the base material, and 200L to 208L steel drums are preferred.
3. High degree of automation: It can completely eliminate the pre-sewing process such as polishing, circle circle and edge spot welding required for semi-automatic seam welding machine, and the subsequent process of trimming and polishing after seam welding, reaching the steel drum The automatic seam welding machine is all high-speed and automatic one-time efficient work. Production efficiency can be up to 5 seconds.
4. Convenient operation: The control of the electronic control system adopts PLC programming controller and man-machine interface, and all Chinese man-machine dialogue. The welding quality is stable, the electrode pressure, welding current, welding speed and other parameters are easily adjusted, and the amount of edge is stable.
5. Reliable and beautiful: the weld seam is rolled through two passes, which further improves the welding quality, and the surface of the workpiece is smooth and beautiful.
6. Stable work: FNT-3×150 high-speed steel barrel automatic seam welding machine for production. Due to constant current control welding current, it can eliminate the influence of external factors on welding quality due to loop resistance and grid fluctuation, and can guarantee 0.5mm internationally popular thin-plate steel barrel welding and domestic 1.5mm steel barrel welding have a large adjustment range and the welding is more stable.
7. Energy saving: The welding power source adopts three-phase secondary rectification welding power source, which has less reactive power loss, the power factor of the welding circuit is up to 95%, the grid load is balanced, the line current caused by the AC welding power source is not large, and the network voltage fluctuates greatly. The impact has improved the electrical environment of other equipment. During the welding process, it is not necessary to consider the current change and the influence of the magnetic field caused by the influence of the metal barrel on the impedance, so that the welder obtains a more stable current, heat and magnetic field. Due to the DC output of the welding power supply, the impact on the power grid is reduced, the welding energy is concentrated, the input power is reduced, and energy is saved.
8. Material saving: FNT-3×150 high-speed steel barrel seam welding machine adopts a new edge welding process. The edge is only 3-4mm, which reduces the material usage compared with the original edge width of 10mm, which saves costs and reduces the cost. The force of the weld is affected, which reduces the amount of processing in the subsequent process.
three. Promotion
At present, the FNT-3×150 high-speed steel barrel seam welding machine has been all produced locally. The products produced in the user's use have reached and exceeded the requirements of the imported equipment, and can gradually replace various domestic and foreign workers. Frequency AC automatic and semi-automatic steel barrel seam welder. Good economic and technical benefits in actual production
(1) Improve the welding quality, the failure rate of the steel drum is reduced from 4% to less than 2%, which greatly improves the quality of the weld and solves the problem of weld leakage.
(2) Energy conservation: Originally used domestic welding machine requires 3 sets of FN150-5 welding machine and 2 sets of 75KVA spot welding machine. One 5KVA reeling machine with a total capacity of 605KVA. The work done with 6 sets of equipment can be completed with only one FNT-3×150 high-speed steel barrel seam welder.
(3) Using new technology to improve production level and reduce labor intensity, the automatic welding machine assembly reel, spot welding positioning, and longitudinal seaming are completed in one machine, shortening the process flow, high degree of automation, and reducing labor intensity. Reduced operator.
For the production of tens of millions of steel drums per year in China and the increasing international demand under the promotion of international trade, the steel drum packaging industry is constantly in line with international standards in product structure and technology. FNT-3×150 high speed steel barrel seam welding machine Has been able to meet the demand for changes in the thickness of steel drums, and will also
Continue to meet the needs of steel drum production in other areas.
Together with the steel drum manufacturing industry, it will realize the development from small-scale production to large-scale grouping and basement, and the development of small varieties to international varieties, and improve and reach a higher level of steel drum industry.
references:
(1). On the development trend of steel drum packaging industry Yang Wenliang
(2). Current status and development direction of steel barrel seam welding machine in China Yang Wenliang
(3). New Trends in the Development of Steel Barrel Products in China Yang Wenliang Xin Qiaojuan
(4). Application and development of automatic seam welding machine for steel drums
Over 10 years of expericence in product development and collection, we have various of designs and packing. We manufacture Shower Curtain and table cloth, including PVC,EVA,PEVA or Polyester shower curtain & tablecloth, the standard size is 180x180cm or customized, table cloth for square and round shape,the size can be customized as customer's requirement. Shower curtain and table cloth not only make your home looks tidy, but more warmth. Tidy Fahsion, Your gentle pursing!
Shower Curtain,PVC Tablecloth,PEVA Shower Curtain,Household Items
Shijiazhuang Tidy Fashion Trading Co.,Ltd , https://www.raincoatchina.com