(Sleeves in flexography-which way to go?) In DRUPA 95, there are about 30 sleeve manufacturers exhibiting and exhibiting their own products. Since then, sleeve technology has developed rapidly and applications have become more It is universal. At present, Rotec has become the world's leading manufacturer of sleeves. In addition, Polywest/Saueressig, Rossini and Stork are world-renowned sleeve manufacturers and their products are also quite good. Occupy a certain market share. After the sleeve technology is applied to flexographic printing, it makes the “replacement of the work piece†simpler and faster. Therefore, it can undoubtedly reduce the cost and save the cost. This is also the main purpose of adopting the sleeve. According to different uses, the sleeve can be divided into the following types: 1, rubber and polyurethane sleeve. They are mainly used as printing plates, especially for the printing of continuous stationery products; if such sleeves are not exposed to image processing, they can be used for coating, glossing and printing in solid areas. 2. The surface is sprayed with a ceramic coating and a sleeve made of a carving process, which is what we call the anilox roller used in flexographic printing. 3. The sleeve used as a printing plate carrier must be unexposed. 4. Adaptor sleeve. The role of such a sleeve is mainly to increase the diameter of the cylinder body and the supporting shaft. 5. Blanket cylinders on offset presses, embossing cylinders in gravure presses and compounding equipment, and applicator rolls used in the coating process. These are also sleeves and can be classified as one. 6. A thin metal sleeve made of nickel. The length of the repeated printing can be unlimited, but it is not suitable for thin printing technology. In addition, there are many other types of sleeves, not listed here. However, only two, three and four types are used in flexographic printing. This article will introduce and discuss the three sleeve technologies. First, the support shaft sleeve is generally installed on the drum, support shaft or mandrel, and is installed through the air cushion. The sleeve system with a conical support shaft and hydraulic expansion (Rossini system) has become a thing of the past and has basically been eliminated. Since the inner diameter of the sleeve is slightly smaller than the outer diameter of the support shaft (0.05 to 0.2 mm), it is necessary to first release the compressed air in the support shaft so that the sleeve can be inflated and then installed and unloaded. The maximum error range of the outer diameter of the support shaft should be controlled within 0.015 mm, and no negative error should occur. The compressed air (6~8 bar) is filled into the air cavity of the support shaft through one end of the bearing. At the same time, there are many specific circular holes or long holes on the surface of the support shaft, which are used to discharge the compressed air. Compressed air forms a cushion layer on the surface of the support shaft, allowing the sleeve to stretch and float on the cushion layer, so that the sleeve can be replaced easily even on a wide flexographic printing press. It is also important that the sleeve rotates in the circumferential direction, so that the register marks can be aligned on the support shaft and the sleeve. This is especially true for presses that cannot automatically determine and return to the zero position. favorable. The Rotec sleeve can also be mounted in left and right inversions. With the sleeve rotating in both directions at the same time, reverse printing can be easily performed. Second, the determination of the position of the sleeve At present, some manufacturers are still producing the internal shape of the conical sleeve, and sometimes even do not need compressed air (cone meshing), the process of this kind of sleeve is simple, but the installation and uninstall are Very strenuous. When the Rotec sleeve is installed, after the air pump is turned off, the air between the support shaft and the sleeve is released, the sleeve gradually shrinks and covers the surface of the support shaft, and finally it is integrated with the support shaft, and the combination is very tight. Strong and seamless. Due to the high accuracy and small error of the Rotec sleeve, it can be guaranteed that it will not shift even if it is used under high tension and high printing pressure for many years. If a narrow-width job is often printed on a wide-format printer, it is possible to cover a portion of the width of the support shaft with a sleeve of a suitable width, so that the cost is lower. In order to mount the narrow sleeve exactly in the middle of the press, the support shaft is equipped with a movable positioning pin. In this case, a ball valve is preferably used at both ends of the support shaft. After the compressed air is charged, the sleeve presses the valve into the support shaft. Third, the compressibility of the inner layer of the compression layer has a great influence on the construction and performance of the sleeve, which makes the sleeve wall thicker. All the tensile deformation of the sleeve can be absorbed by this compressible inner layer. However, it is self-evident to ensure close contact with the supporting shaft. Rotec sleeve structure: soft glass fiber inner layer (GFK), elastic compressible layer, light polyurethane, hard polyurethane outer layer. When the sleeve is installed, only a very thin, compressible layer will deform. For the anilox roll, compressibility and protection of the ceramic layer are very important, because cracks will appear when the surface of the sleeve expands to a certain extent, ink and cleaning agent will penetrate into the metal layer, causing oxidation reaction. Therefore, Rotec anilox roller sleeves generally have a hard aluminum sheath, the purpose is to absorb the centrifugal force. In order to determine the true and accurate diameter size of the sleeve, it is recommended that after the sleeve is installed, it is best to stand still for five minutes to ensure that all the compressed air is discharged and the sleeve gradually adapts to the support shaft and stabilizes. In addition, printing speed is also a very critical issue. The fringes caused by the machine's vibration will have a negative impact on printing. Most printers know this; but in fact, due to the vibration of the supporting shaft along with its own operation, the printing speed is largely Depending on the flexibility of the support axis, most printers often do not know enough about this. The degree of flexibility depends on the ratio between the diameter of the support shaft and the length of the support shaft. The higher the bending strength of the support shaft, the more vibrations are absorbed.
It is a luxury Inversion Table , the Home Using Gym Inversion Table
is a Plastic Back Inversion Table .The inversion table has safety belt . It is
also a Folding Inversion Table ,when you stop sports , you can fold it and don`t
occupy much space .. The plastic parts and steel parts of the back are big and
stronger . So it is can be used for long time . The machine side has two
plastic parts and you can stick your logo there . The back has a smaller
cushion and can massage neck when handstand . The luxury inversion table also
has a luxury equipment to fix feet , you only need to press the button/switch.
It is is easy to use . PLS remember it the model is XJ-CI-03V.
XJ-CI-03V
|
SPECIFICATION
|
G.W
|
35KGS
|
N.W
|
33KGS
|
Max Weight
|
150KGS
|
Meas
|
128*76*21 CM
|
Max Height
|
198CM
|
Size
|
130*79*152CM
|
QTY
|
1PC/CN
|
Ctn
|
135PCS/20`FT
|
280PCS/40`GP
|
330PCS /40`HQ
|
|
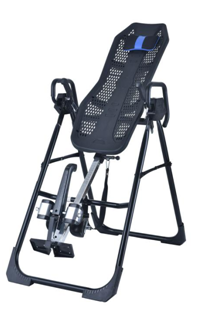
Home Using Gym Inversion Table
Home Using Gym Inversion Table,Power Inversion Table,Inversion Table With Massage Cushion,Gravity Therapy Inversion Table
ZHEJIANG MEIER FITNESS EQUIPMENT CO., LTD , http://www.chinameier.com